A bit of history (part 14) – Head scratchin’ time
- ainsworthashley
- Aug 17, 2017
- 5 min read

Recalling back to the initial dyno session with Dave Rowe, he noted that he could hear a “bearing type” noise through his earphones…at the time we assumed a wheel bearing, although we never found anything wrong with either rear bearing. I pretty much forgot the comment after this…
However, the more I drove the car, the more I became aware of a “whirring” type noise behind me, on the timing end of the engine. You could hear it best in the cabin with some of the other engine noises muffled, and it seemed to change frequency in relation to engine speed.
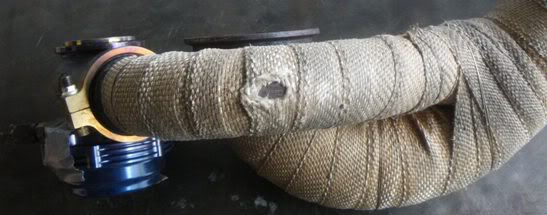
As I had gone through the various teething issues I had been keeping an eye out for any potential causes, such as could it be the noise of boost leaking through the silicon pipe on the turbo that kept splitting? Could it be the crack in the exhaust manifold heat shield vibrating? Could it be the noise from where the exhaust down pipe had been rubbing on the bulkhead heat shield?
But every time I fixed one of the issues, the noise persisted…and now I was out of other things that needed attention, it was time to specifically investigate the mystery noise.

First up I dropped the engine oil and inspected it, I noted a slight metallic sheen to it, and a collection of grey sludge on the magnetic sump plug. I gutted the oil filter and found a liberal scattering of metal in there…oh dear…(or something to that effect).
I stuck the car on a trailer and headed to Tony’s place, he took a look at the sludge on the sump plug and confirmed this was assembly lube that he had used when building the engine, so no big deal.

We found that the metallic flakes were magnetic, so not aluminium and probably not from the bearings…additionally there were no signs of any copper either.
The chunks of metal also looked too big to be from running in the pistons rings, when normally give more “powdered” size remnants.
So we lifted the cam cover and inspected each cam journal in turn, and it all looked brand new still…so we’re stood there in the July sunshine scratching our heads…what could this be? Theories we came up with being:
Contamination from the oil cooler if it hadn’t been adequately flushed (it could even be, at a stretch, remnants of the original running in oil trapped in the oil cooler if we assumed it hadn’t been flushed as part of the first oil change).
Turbo bearings? Seemed unlikely given there was no change in shaft play.
Camshaft buckets breaking up? Again, seemed unlikely as you’d expect lots of aluminium from the cylinder head itself before the buckets themselves broke up? Also, if they were breaking up where they contact the valves you’d expect a lot more top end tapping, which wasn’t the case at all.
Side wear on the big ends? Seems unlikely given the liberal clearances on these engines.
Oil pump eating itself? From what I know this is pretty rare, and it was a brand new Toyota pump…but it would explain the debris in the filter, with no damage to the cam journals as the filter would catch it all.
Tony’s advice was to continue driving the car for another couple hundred miles and then check the new filter, if it’s clean we can assume the debris has flushed and gone…if there’s fresh metal in there we would drop the engine and rip it apart.
I was happy with Tony’s advice, but part of me was close to just giving in a selling up…this was yet another issue in what was becoming the saga of my car project! I decided to leave it all alone for a while and concentrate on stripping down the naturally aspirated track car, during which time I formulated a new plan…

I had already decided I wanted this car to handle and stop as well as the track car had, but I also wanted to keep it as a nice car to drive on the road- the track car had become a bit too bare bones hardcore for road driving, especially from a noise perspective. So I decided to retain as much of the interior as I could, so it still looked nice, but with all extraneous weight removed (such as sound proofing).
I would fit my bucket seats and harnesses, along with the roll cage…but I would keep the dashboard as standard looking as possible. I also decided I wanted to fully re-wire the car, I was never 100% happy with the state of the wiring after the new ECU and data logger had gone in, it simply wasn’t tidied up enough for me…this car needed to look properly finished.
I also wasn’t happy with how the Race Technology dash was working, it was very glitch and never seemed to be able to display decent speed reading…the RPM reading would also occasionally go mental, triggering all sorts of alarms…very annoying. (It turned out that this was pretty much all down to the installation, where it was connected to the ECU via a serial interface instead of using CAN. It was also using GPS to derive speed, which would lose signal occasionally…all in all a very error prone setup).
I have always wanted to fully wire a car from scratch, and as this project was all about learning, it seemed a good opportunity…with the added bonus of adding lightness by removing all non-essential wires. To aid this I was lucky enough to be offered some very very discounted MoTeC goodies…namely an M880 ECU (to replace the M400), a Sports Digital Dash and Data logger, and a Power Distribution Module (PDM).

The major bonus was that all of this kit would communicate together using CAN, and I would finally have a robust, fully integrated system in the car…
[MoTeC Products:
M400 & M880 – these are both examples in the preceding generation of ECUs before MoTeC’s latest M1 series, the M400 supporting up to four injector engines, and the M800 supporting up to twelve injector set ups. The M880 represents the top of the range, coming with advanced features such as traction control, anti-lag, etc. as standard…and it uses an Autosport connector.
SDL – this is part of the older range of MoTeCs digital display/ data logger combinations, being the Sports Dash Logger. It communicates via CAN, and has its own set of inputs and outputs which you can programme, as well as acting as a data logger.
PDM32 – Power Distribution Module: being a solid state replacement for all the fuses and relays used in most cars. This is both more reliable, and more flexible as you can programme the parameters for the various outputs, for example maximum current settings. The 32 refers to the number of separate output channels on board, and again- this unit communicates to the ECU and SDL via CAN.]

December 2012 saw my brother helping me swap in the new ECU so that I could offload the M400 and get some cash back, this was a pretty straight forwards exercise involving de-pinning one ECU plug and cross referencing to the other ECU, before repining the new ECU plug.
This was my first exposure to motorsport spec wiring, notably the use of decent crimp tools and Autosport connectors…little did I know how very closely acquainted I would get with these in the future!
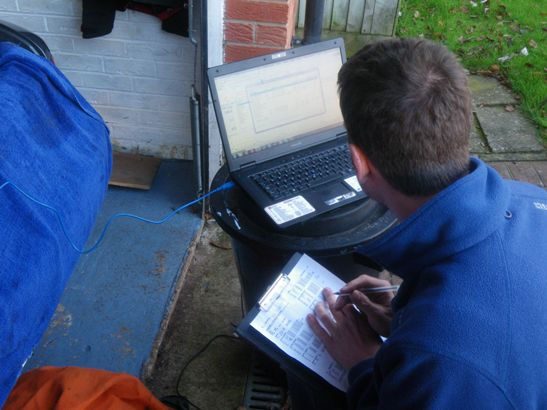
As part of this swap we removed the wide band lambda controller I had used, as the new ECU could control the sensor directly - so giving me some more kit I could sell off…
We are now in early 2013, almost five years since I bought the car, and the next thing on my list is to pull the engine out to try and locate the cause of my mystery noise…
Comments