A bit of history (part 13) – A thought for fuel
- ainsworthashley
- Aug 17, 2017
- 5 min read
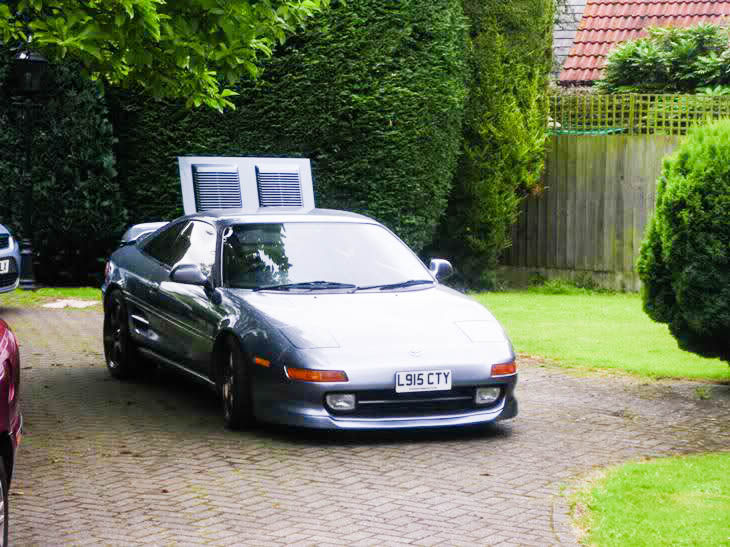
Having installed the larger turbine housing on the turbo, the car would need to be remapped before I could drive it in anger again. Before I could do this I had a couple of concerns to address, the first being the fueling system.
When we last visited the dyno with Dave Rowe he had noticed that the fuel pump sounded like it was cavetating, we had swapped in a new pump for the second dyno day and everything was sweet. However I had kept an eye on things since mapping, and I was noticing that the fuel swirl pot in the boot was getting very hot, and as it did so the new fuel pump was getting louder.

The fuel system on the car was the same as when I originally imported it, basically a standard pump in the fuel tank pumping fuel into a swirl pot in the boot. This swirl pot provided fuel to an external high pressure pump, which pumped fuel to the fuel rail, and then back into the swirl pot…with an overflow return line from the swirl pot back to the tank.
Looking at this setup it was apparent that the fuel was being pumped round and round the fuel rail and the swirl pot, and basically soaking up engine heat the whole time…not ideal!
I considered various options, such as using an in line fuel cooler, or even modulating the high pressure pump in relation to engine load…but more investigation was required. This is the point that another character is introduced to the story: Peter Gidden.

Peter runs a small workshop in Yorkshire (SBITS) that specialises in Toyota MR2s and Celicas, these days he is a one man band and does all sorts from servicing to full engine builds. At the time Peter was looking after/ building/ modifying Simon Hick’s drag racing MR2, which was producing excellent results at the Brighton Speed event.
I contacted Peter as I knew he’d thought long and hard about the fuel system for Simon’s car, and I was glad I did…Peter (whilst not the most organised of people!) is a kindred spirit in his approach to all things automotive. He really likes to understand how things work, and why various things work or don’t work…this often leads him/ us down rabbit holes as we seek to understand what is going on in a given situation, where most folk would simply accept that something was fixed and move on…we were both equally fixated on why it was fixed!
Over the years we’ve spent many hours discussing various technical issues, and I always enjoy these discussions as invariably one, or both of us, will learn something new. As you can probably tell, Peter has become a good friend over the years, and will feature going forwards in this story!
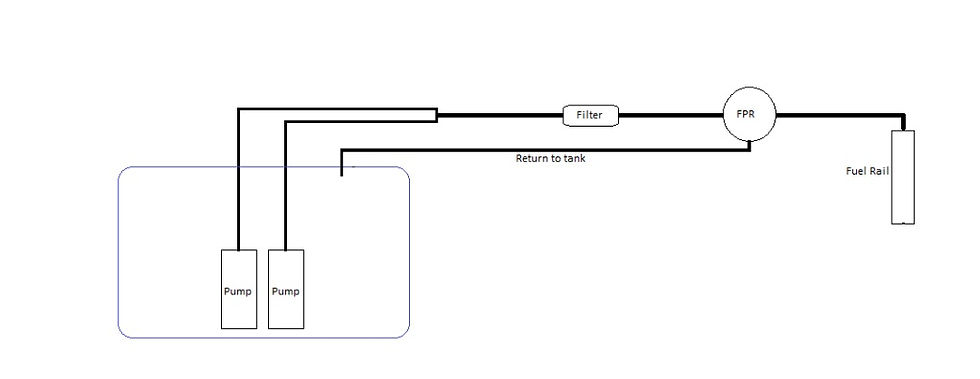
Anyway- Peter described the system he’d used on Simon’s car, which was a twin pump setup in the fuel tank, leading to an Aeromotive fuel regulator, with a dead-head fuel rail setup. So basically lots of fuel pumped to a regulator, which then feeds a specified pressure to the fuel rail, and returns surplus fuel to the tank.
I liked the idea, but was nervous of a dead-head setup…I know it was proven approach, but I was nervous of the idea of fuel staying in the fuel rail at lower engine loads and having a chance to warm up before being allowed into the engine by the injectors.
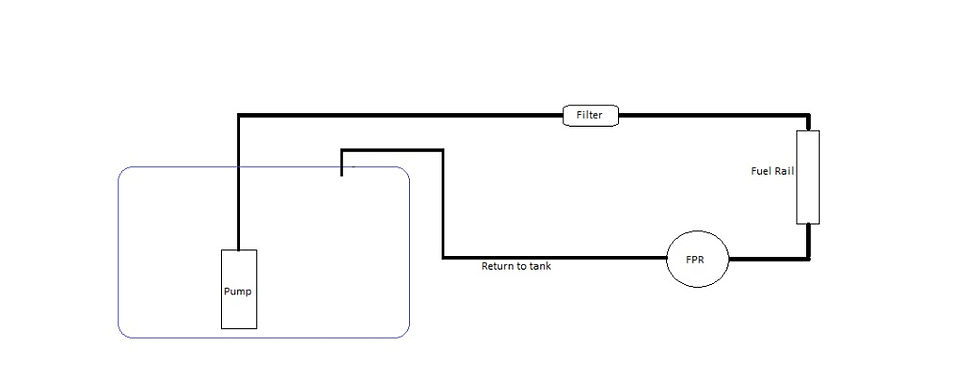
The alternative setup was to flow the fuel from the tank directly through the fuel rail, with a regulator after the rail moderating pressure, and returning fuel to the tank. This meant that fuel would be continually moving in the fuel rail, and returning to the tank…so in theory the fuel in the tank would start to warm up (as it had done in my swirl pot), but the vastly increased volume absorbing this heat should make this less of an issue.

I also discussed this with Tony G, and he suggested I try out one of the new Walbro high capacity pumps- they had just released the 440lph pump, which was smaller and quieter than the Bosch 044 I had been using. Taking his advice, and Peter’s I ended up with a shopping list, which duly arrived from friends in the US as a gift, happy days!
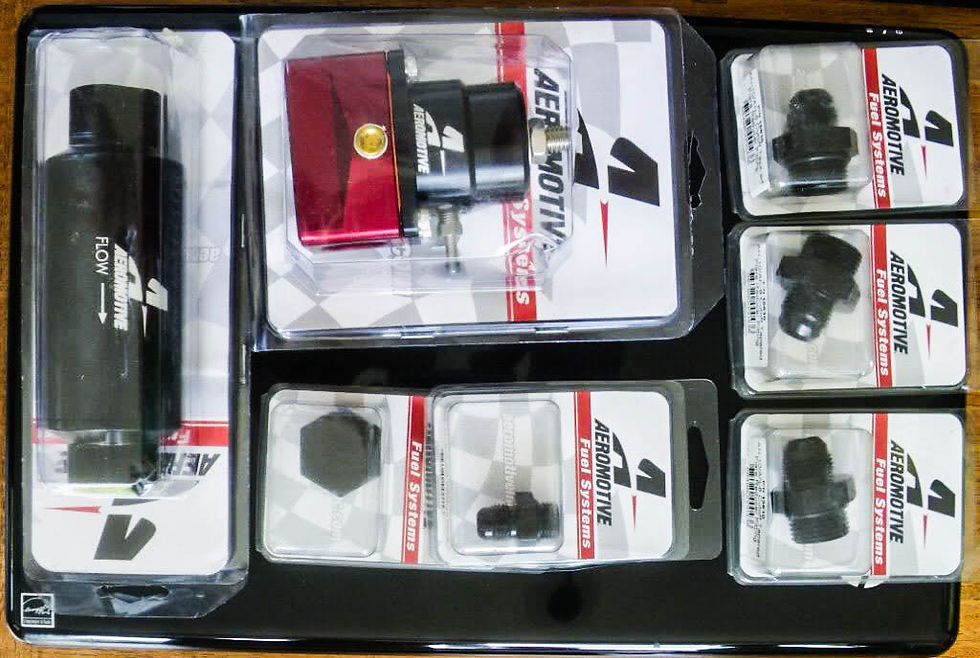
Then onto the installation…time to get my hands dirty again and pull the fuel tank out of the car…so over to Dad’s workshop we go…
This time I felt far more confident attacking the car, although I was still surprised by just how much kit had to come out in order to get the fuel tank out! After a quick shower in antifreeze, I cleaned myself up and recharged with a brew before cracking on...I think you have to have worked first hand on an MR2 to understand just how much a painful job it is removing the fuel tank, but eventually I was rewarded for my efforts...

I removed the original fuel pump from the tank and was surprised to see that the replacement, much higher flowing pump, was significantly smaller...in fact I had to go double check I'd actually ordered the correct part. But sure enough it was correct, which made the in tank install far easier than I had expected.

The install meant modifying the standard fuel pump hanger to accept significantly larger fuel lines, and then teaching myself how to make up braided Goodridge lines…a good learning exercise involving making lots of small holes in my thumbs…

It was then (eventually) a case of putting everything back in the car, including the new lines and pressure regulator, before the test fire…which went very well and she started on the button…oh yes, confidence boosting stuff!
[Fuel pressure considerations.
The fuel pressure regulator’s job is to provide the fuel pressure you request to the injectors in the fuel rail, and it does this by venting excess pressure (fuel) back to the fuel tank. The first thing to consider when deciding what this pressure should be is the relationship between pressure and flow…

At lower pressures you get more flow, and as pressure increases flow drops…something that wasn’t initially obvious to me until I thought it through! Looking at this relationship, it would seem that ~20psi would give maximum flow, but you need to balance this with adequate pressure across the injectors for decent operation. On this basis ~35psi seemed a sensible starting point.
The next consideration is what happens on a forced induction engine when boost pressure rises, all things being equal this means that the inlet side of the injectors now see a higher pressure, and so the pressure gradient across the injectors has decreased (fuel pressure stays constant at entry to injectors, air pressure increased on exit of injectors).
To compensate for this, the fuel pressure regulator has a vacuum line connecting it to the inlet manifold, whereby it will then increase fuel pressure in a 1:1 relationship with manifold pressure; i.e. as boost goes up, so does fuel pressure by the same amount. This preserves the pressure gradient acorss the injectors, and ensures they are functioning as intending at all boost pressures.]

I dialed in the base fuel pressure at idle based on some advice from Bob Hatton, and I was set to book a mapping session with Dave…time to see what impact the larger turbo housing would have…
…or so I thought!
Comments