A bit of history (part 8) – 2.2 litre goodness, and some waffle about compression ratios
- ainsworthashley
- Aug 9, 2017
- 7 min read
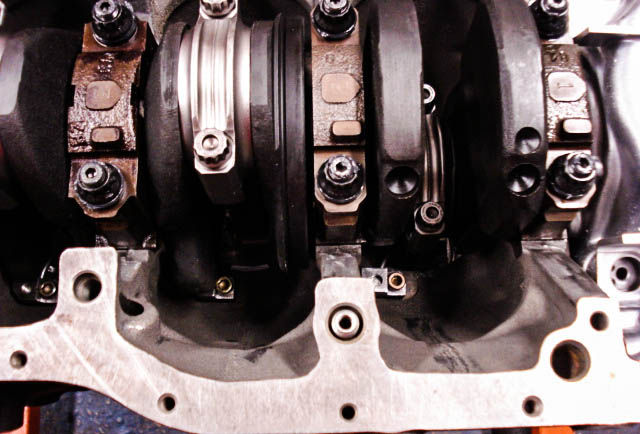
Following Matt’s shock offer of a stronger Toyota 5S block, it took me a while to justify building yet another engine for this project…but the advantage of a stronger, larger capacity engine was too appealing. I did the maths, and taking into account the amount I would get for my current block (with a buyer already lined up), plus the funds from selling the HKS turbo kit I had, it would be possible if I saved hard.
I had the advantage that I had a while to buy the parts for the new engine, which would give me longer to save…
So decision made, and a new shopping list was drawn up:
CP 87.5mm forged pistons (8.5:1 compression ratio)
3S Eagle forged con-rods
ARP main bearing studs (and I was keeping the ARP head studs I already had)
Morosso extended oil sump
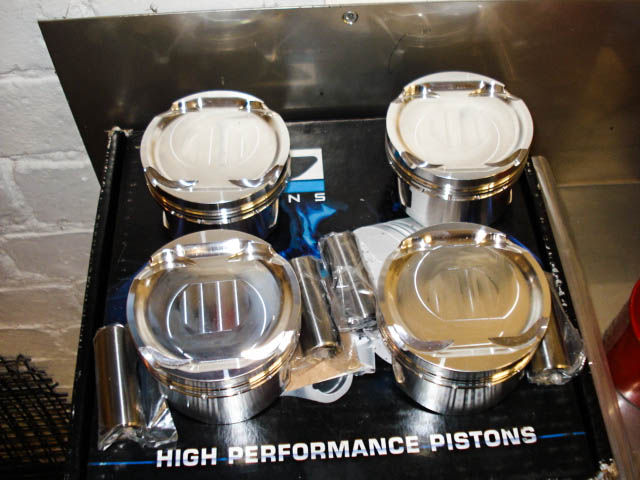
Next up was to agree who would build the engine as Tony Gibbons had now left his position as Rogue’s engine builder. Tony is a great guy, and really knows his engines and gearboxes, last time I saw him he was still partway through building an awesome Manta drag car, fully caged with a crazy compound turbo charged setup…that reminds me that I really do need to go and catch up with him, it’s great that there are so many creative folk in the UK building crazy cars in their sheds- love it!
Anyhow, the issue was Tony didn’t work for Rogue anymore, so I had to negotiate him to build the engine, and then for Matt to do the rest of the build…so splitting the build process, something we are frequently warned against in case things go wrong and neither party wants to accept responsibility. Ah well, I wanted Tony to build the engine, so I had little choice…

Tony had some nice ideas for the build, such as using oil squirters (nozzles that squirt oil at the underside of the pistons to aid cooling) which are not a stock part of a 5S block. The 5S crank shaft needed modifying by a machine shop (the big end bearing journals were turned down to fit 3S rods, and the flywheel holes were adapted to match a 3S flywheel), and was then nitrided to harden it.
I had considered having the crankshaft lightened and knife-edged (as I had with the 3S crank), but Tony was confident that it simply wasn’t worth the cost on this type of build where I wouldn’t be pushing for crazy rpms, the added engine volume would ensure the engine made grunt low down to avoid the need to rev it’s nut off!

The pistons had minimal machine work doing to them, and the final compression ratio of the engine was measured and calculated at 8.3:1 using an HKS 1mm head gasket (and so preserving the stock squish clearance). I was really happy with this as a starting point for the engine, and I was confident I could give the build some decent boost this time...
Tony then built the engine up, dialed in the cams and sent it off to Matt to work his magic with…happy days!
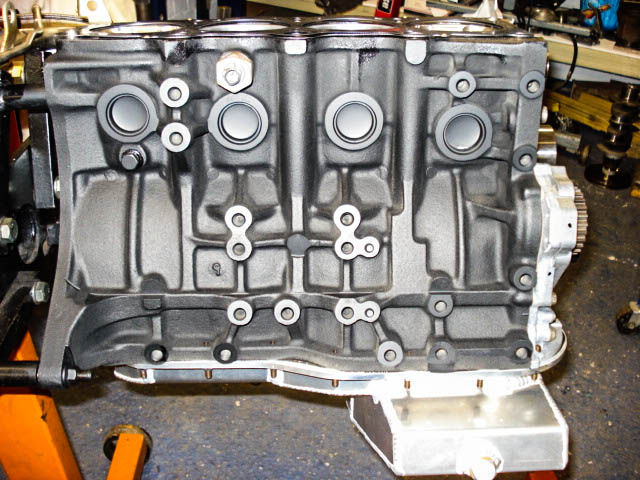
At this point I feel the need to get technical and talk about compression ratios, which I mentioned a couple times above…this is likely to either be too simplistic, or overly detailed for most readers, so feel free to skip on! Also forgive anything I get wrong, I’m not an expert…but I am always keen to learn, so let me know!
[What is compression ratio, and why do we care?
In order to explain this to those who don’t know how engines work we need to go to the basics of four stroke motors. An engine is basically an air pump, with pistons going up and down the cylinders attached to a crank shaft- this up and down motion is transferred into rotation of the crank shaft, which drives the gearbox and makes the wheels spin.
Each cylinder has valves to let air in and out and the relevant times.
So far so simple…
One engine cycle consists of the piston moving down the cylinder with the inlet valve(s) open and “sucking” in a mix of air and fuel. The valve(s) then close and the piston moves back up the cylinder compressing this air/ fuel mixture.
Towards the top of the pistons travel up the cylinder the spark plug fires, igniting the air/ fuel mixture which then starts to burn, this creates pressure that pushes against the piston as it travels back down the cylinder, and is what creates the engine’s torque (the harder the combustion forces push down on the piston, the higher the torque the engine will produce).
Finally the piston travels back up the cylinder with the exhaust valve(s) open, pushing the combusted gases out of the engine, ready to suck new air/ fuel back in and repeat the cycle.

OK- so that’s the four stroke cycle, next we need to consider how the timing of the spark effects this cycle…
When the spark plug fires the air/ fuel mixture in the cylinder does not instantly explode, rather there is a tumbling flame front that burns evenly across the mixture…and this takes time. So the spark plugs typically fire before the piston is at the top of its travel up the cylinder in order to allow the combustion process to start, and give peak forces when the piston is going back down the cylinder to push it.
If the spark fires too early, the combustion process (which has started too soon) begins producing higher pressures before the piston is travelling back down the cylinder, and extreme pressure/ heat is created in the combustion chamber. This can cause pockets of the air/ fuel mixture to start to explode in an uncontrolled manner, which causes very sharp, high forces which are capable of damaging the pistons, the crankshaft, and the engine itself…this is termed detonation.

On the other hand- if the spark fires too late, then the volume the combustion forces are occurring in is increasing as the piston is travelling down the cylinder, and so torque is lost as less pressure is available to push the pistons down. This also leads to the engine experiencing the heat of combustion lower down in the cylinders, and even in the exhaust manifold and the combustion process has not been completed before the gases are pushed back out of the cylinder again.
So why have I bothered to explain this…?
Well, we were talking about compression ratio in the design of engines, so what is compression ratio?

Put simply this is the volume in the cylinder with the piston at the bottom of its travel, in comparison to the volume of the combustion chamber with the piston at the top of the cylinder. So a 9:1 compression ratio indicates that there is 9 times the volume in engine with the piston at the bottom of the cylinders, compared to when it is at the top…so ignoring combustion (and volumetric efficiency) this is the amount the gases in the engine would be compressed before ignition.
Why does this matter? Well, on a forced induction engine, where we are forcing more air/ fuel into the engine, we are already effectively increasing the pressure of compressed mixture in the engine…i.e. if we have 1 bar of boost going into the cylinders (again ignoring volumetric efficiency!) then we have doubled the mass of air/fuel mixture in the cylinder before the piston starts to go up the cylinder, and hence we have doubled the static pressure of compressed mixture with the piston at the top of the cylinder...so in our 9:1 example, we now have 2:18 compression going on- a significant increase in pressure in the combustion chamber before ignition.
Given that one of the causes of detonation is extreme pressure, then this situation has increased the likelihood of detonation before we have even considered ignition timing.
As a result the old-school thinking for forced induction engines was to drop the static compression ratio as you design an engine for more boost pressure, so reducing this mechanical pressure increase…makes sense?
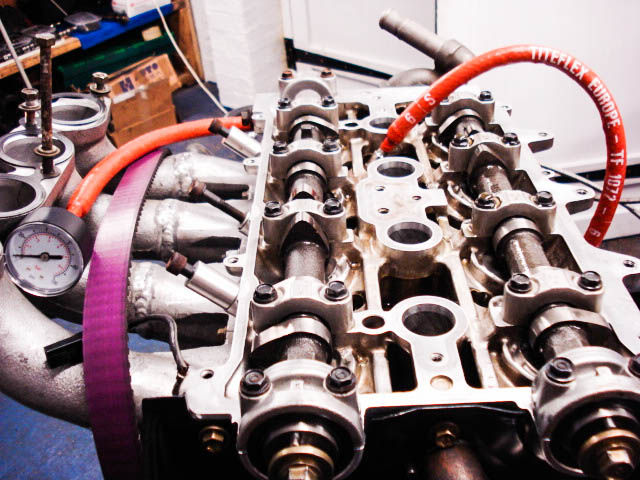
Well (like with most things) modern thinking has changed somewhat, and with modern ECUs giving vastly improved control over fuelling and ignition, there has been a move away from the old-school approach. But how do we avoid detonation with lots of boost without reducing compression ratio?
The answer is not simple, but it comes down to more fuel in the air/ fuel mixture (which cools the combustion chamber, so helping avoid detonation), and delaying ignition (and so avoiding the extreme combustion pressures that lead to detonation). In fact, in the most modern direct injection engines, we can actually phase the delivery of fuel into the cylinder during the combustion process itself to help create an even burn, and avoid detonation which seems to allow very high compression ratios to be used.
Another option is to use a higher octane fuel, which has increased resistance to detonation, and one of the major reasons why race fuel produces higher power- you can use more ignition advance without detonation.

But, and to bring this back on topic! Let’s remember I am playing with an engine design from the 1990’s, when Toyota deemed it necessary to decrease the compression ratio of its engines when they used turbos. Add to this my suspicons that my first engine had died due to extreme heat (and maybe detonation?), presumably as a result of pushing too much boost into the cylinders, and so having to overly retard ignition.
Why did this kill the engine? Well remember the effects of overly retarding ignition- peak combustion temperatures are now experienced further down in the cylinders. And this is in an engine design with concerns over the quality of the casting involved in the manufacture of the cylinders themselves!
In a nutshell- the 3S / 5S engines were not designed to run high boost, with high compression pistons, and there are concerns (in my mind) about their strength to deal with keeping a high compression ratio and retarding ignition, as this exposes the cylinders to extreme temperatures.
And so…hence the reason why I took the decision with this engine build to swap from 9:1 compression pistons to a final compression ratio of 8.3:1 to help reduce the amount of ignition retardation required, and to help improve engine reliability…and here ends the lesson, and apologies for the gross over-simplification of my explanations!]
Comentários