A bit of history (part 6) – Back to the turbo
- ainsworthashley
- Jul 24, 2017
- 5 min read

I don’t think hindsight is quite the wonderful thing folk make it out to be, sure it’s great to learn the lessons of past mistakes, but what I wouldn’t give to have been able to take advantage of this knowledge in the first place!
2011 finds me with my GTS on the road, and having been ‘safely’ (or should we say conservatively) mapped with relatively low boost (1.2bar), it was proper fun to drive…my problem was it just wasn’t as shockingly fast as it had been before, and I was missing the thrill. My continued addiction to boost was starting to take over, and withdrawal was kicking in- slowly but surely…
As I stated before, in hindsight, I should have left the car as it was when I first bought it, 350bhp with 1bar of boost was ample, especially if I had left the smaller camshafts in there. But, it seemed I had taken things too far now and I was left trying to work out how to move forwards.
The HKS turbo on the car has a relatively small exhaust turbine side (the wheel that the exhaust gases spin up as they push through it), this means as soon as I started to up the boost for more fun, the small housing became a restriction to the exhaust gases trying to exit the engine, and as a result the pressures in the exhaust manifold rose and everything started to get way too hot.
Injecting water and methanol had helped cool things down a bit, but I wasn’t comfortable relying on this, especially as the ECU I had lacked the functionality to automatically turn boost down when things started to go wrong…so I was risking killing another engine.
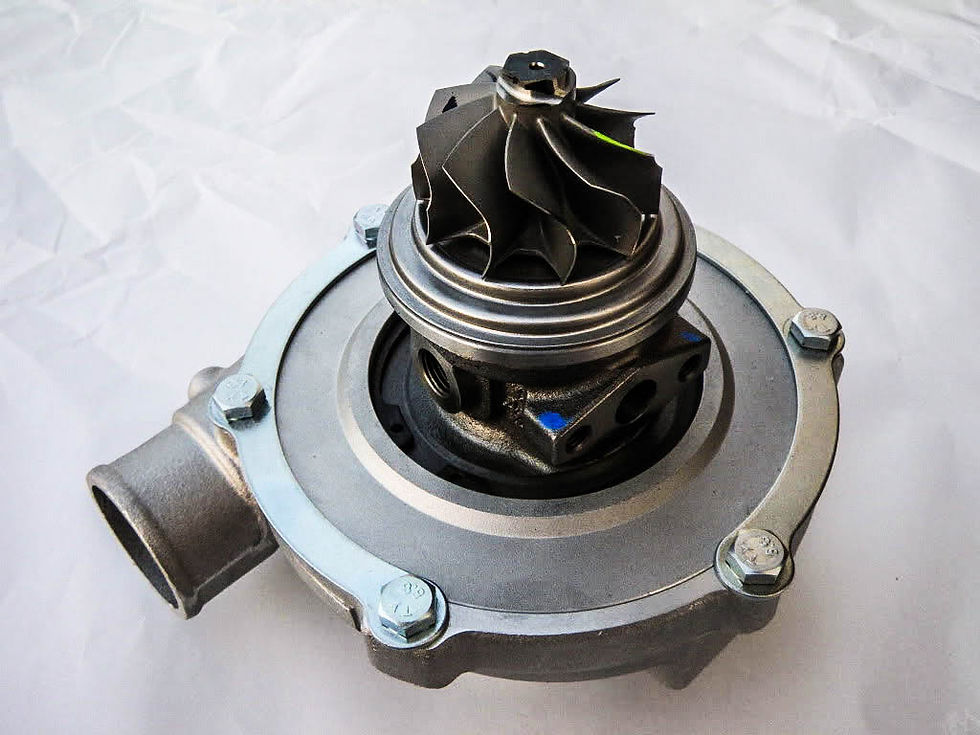
So what to do?
Well, probably what most people would do, I looked at the builds other people had done in the past, and I tried to follow a more proven path. Less reliance on ‘specialist’/ developmental knowledge, and more copying tangible, proven approaches…
Warning: this gets a bit heavy on technical detail now…
[The first issue to address was the turbo, and I opted for the well proven Garrett GT3076r. This has a mid-sized exhaust turbine wheel (larger than the HKS turbo I was struggling with), coupled with a 76mm compressor wheel (the impellor that pulls air in through the air filter, and compresses it to make additional pressure entering the engine…i.e. boost). Investigation showed that this compressor wheel was capable of producing up to ~480bhp on these engines, which was more than I was aiming for, so should have been plenty sufficient.
With these turbos you can choose the dimensions of the exhaust housing (A/R ratio), with a smaller ratio effectively being a smaller entrance for the gas into the turbine wheel itself, so starting the wheel to spin earlier (less turbo lag), but then becoming a restriction earlier (and so causing exhaust pressures/ temperatures to rise). So there is another decision to make- less lag, but lower top end power (as temperatures will get too high again), or more lag and more top end power.
I was happy with ~400bhp, and as such preferred to minimise lag as much as possible- so opted for the smallest housing Garret make, the turbine wheel was already bigger than the HKS turbo, so I should (in theory) make as much power as I did before, but without killing the engine with excess heat.]
Right- so long story short, we now have a new turbo!

Next up we need something to bolt the turbo to, and the old exhaust manifold was too small for the new turbo. I had seen a manifold made by an American company called Full Race a few years earlier, and I’d dreamt of owning one since- the quality of the workmanship was outstanding…more like a piece of artwork!
It took a while to persuade myself due to cost, but in the end I got in touch with them, and shortly thereafter one arrived all the way from sunny Phoenix, Arizona.
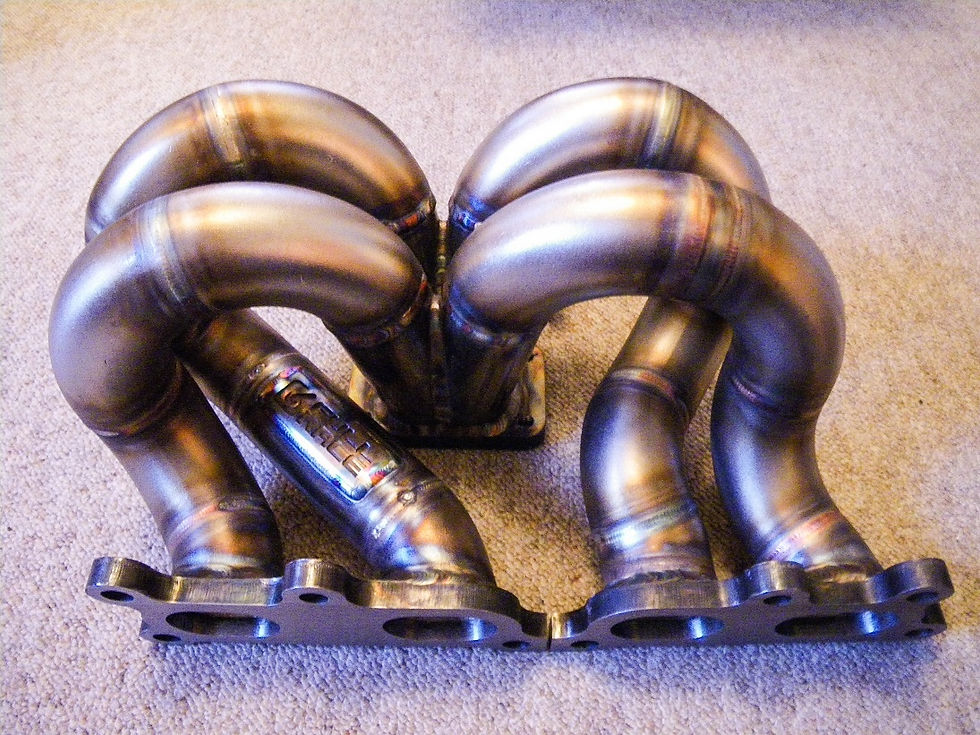
One of the first things I checked was the alignment from the manifold into the turbo, which was an eye opener! I had a steel gasket to aid comparison, and the Full Race manifold was spot on…it was the Garret turbo that was off center, and unsymmetrical.
Quality casting work by Garret!
I wanted to avoid any step in the join between the two, and so had the turbo ported to match the manifold…no point in using quality parts if you are going to ignore the details that will potentially create turbulence in the flow of gases into the turbine wheel.

I had also been warned about gaskets blowing out on this joint, so after seeking advice I decided not to use a gasket, but rather face fit the two together and use pins to ensure they were properly aligned…we also drilled out the standard stud holes to allow larger studs to be used to clamp the two together.
Given my concern regarding the temperatures in the exhaust manifold (having killed my last engine), I wanted a way to keep an eye on them as the car was running. You can measure temperatures after the turbo, but this is only ever an estimate for what is happening in the turbo itself…so I ended up fitting temperature sensors to the manifold, which would give me very accurate data as to what was happening in there.
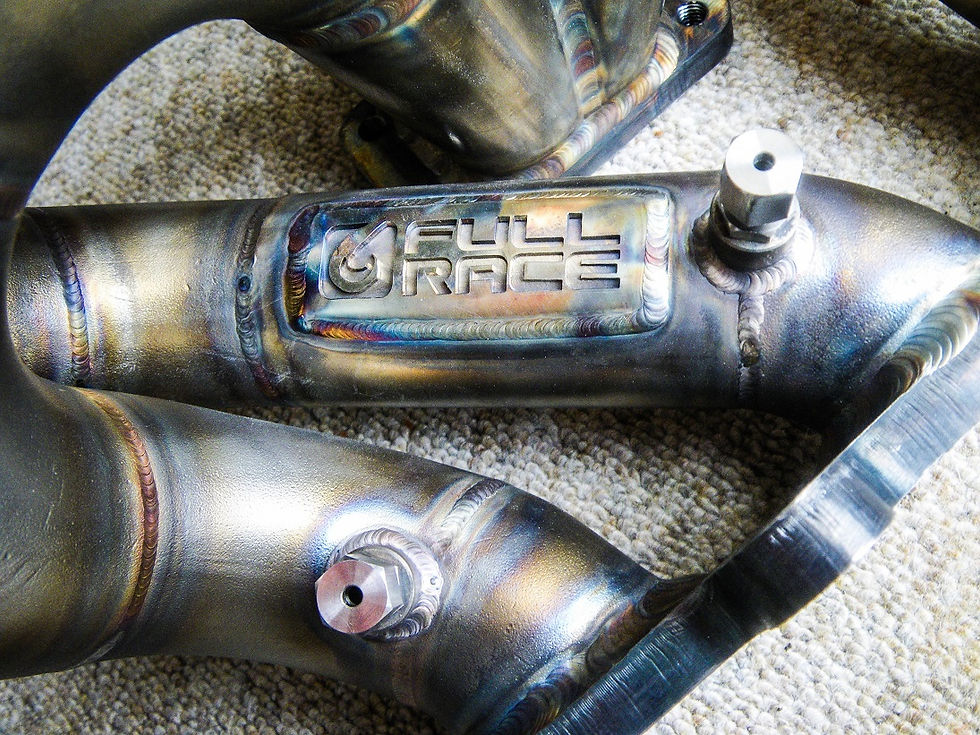
The risk of this approach is that temperature probes do degrade over time in excessive heat, so the plan was to only fit these during mapping sessions, and to calibrate the temperatures in relation to the permanent sensor fitted after the turbo. That way I could remove them most of the time, and use the permanent sensor as a warning device.
The final addition was a new waste gate to control boost levels, and for this I opted for a Tial MVR gate, being suitably larger than the HKS unit it replaced.
Finally, I sent the manifold and turbine housing to Zircotec for ceramic coating- this process creates a thermal barrier on the outer surfaces of the items which acts as an insulator, so helping keep any internal heat inside the items and reducing the amount that radiates into the air around them.
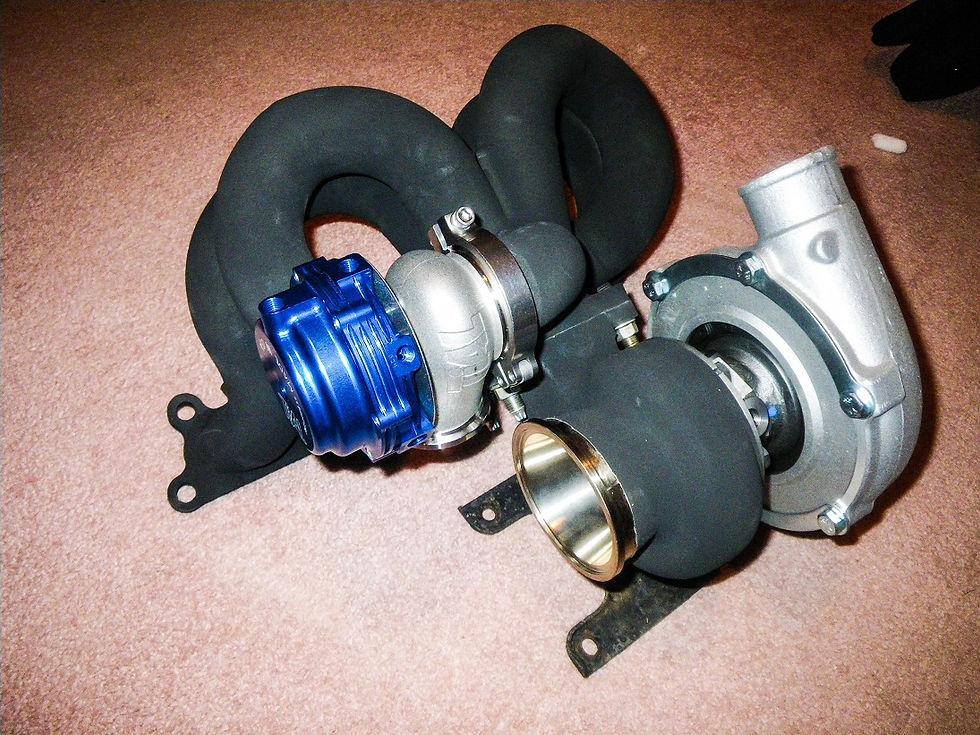
This serves two purposes:
- Firstly it helps control the temperatures in the engine bay (as the exhaust heat is kept in the exhaust)
- Secondly it aids the turbine wheel to generate kinetic energy (as the higher the pressure ratio across the turbine wheel, the more energy you put into it…and more heat equates to more pressure)....
......it’s also quite pretty…...
Comentários